В этой статье отсутствует информация о терминологии: SLM, DMLS, DMP, EBM, SHS . Ноябрь 2020 г. ) ( |
Селективное лазерное спекание ( SLS ) - это метод аддитивного производства (AM), который использует лазер в качестве источника энергии для спекания порошкового материала (обычно нейлона или полиамида ), автоматически направляя лазер в точки в пространстве, определяемые 3D-моделью , связывая материал вместе, чтобы создать прочную структуру. Это похоже на селективное лазерное плавление ; это два экземпляра одной и той же концепции, но отличаются техническими деталями. SLS (как и другие упомянутые методы AM) - относительно новая технология, которая до сих пор в основном использовалась для быстрого прототипирования и длямелкосерийное производство комплектующих. Производственные роли расширяются по мере улучшения коммерциализации технологии AM.
История [ править ]
Селективное лазерное спекание (SLS) было разработано и запатентовано доктором Карлом Декардом и академическим советником доктором Джо Биманом в Техасском университете в Остине в середине 1980-х годов при спонсорской поддержке DARPA . [1] Декард и Биман были вовлечены в создание новой компании DTM, созданной для разработки и производства машин SLS. В 2001 году компания 3D Systems, крупнейший конкурент технологий DTM и SLS, приобрела DTM. [2] Последний патент на технологию SLS компании Deckard был выдан 28 января 1997 г., срок его действия истек 28 января 2014 г. [3]
Аналогичный процесс был запатентован, но не получил коммерческой реализации компанией RF Housholder в 1979 г. [4]
Поскольку SLS требует использования высокомощных лазеров, его использование в домашних условиях зачастую слишком дорого, не говоря уже о том, что оно может быть опасным. Стоимость и потенциальная опасность SLS-печати означает, что внутренний рынок SLS-печати не так велик, как рынок других технологий аддитивного производства, таких как Fused Deposition Modeling (FDM).
Технология [ править ]
Технология аддитивного производства слоев SLS включает использование мощного лазера (например, углекислотного лазера ) для сплавления небольших частиц порошка пластмассы , металла , керамики или стекла в массу, имеющую желаемую трехмерную форму. Лазер избирательно плавит порошковый материал путем сканирования поперечных сечений, созданных на основе трехмерного цифрового описания детали (например, из файла CAD или данных сканирования) на поверхности порошкового слоя. После сканирования каждого поперечного сечения слой порошка опускается на один слой, сверху наносится новый слой материала, и процесс повторяется до тех пор, пока деталь не будет завершена. [5]
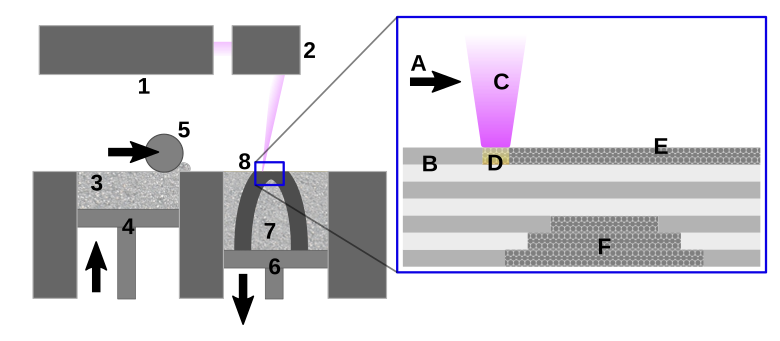
1 Лазер 2 Система сканирования 3 Система подачи порошка 4 Поршень подачи порошка 5 Ролик 6 Рабочий поршень 7 Производственный слой порошка 8 Изготовляемый объект (см. Вставку) A Направление сканирования лазера B Частицы спеченного порошка (коричневое состояние) C Лазерный луч D Лазерное спекание E Предварительно уложенный слой порошка (зеленое состояние) F Не спеченный материал в предыдущих слоях
Поскольку плотность готовой детали зависит от пиковой мощности лазера, а не от продолжительности лазера, в аппарате SLS обычно используется импульсный лазер . Установка SLS предварительно нагревает сыпучий порошковый материал в порошковом слое несколько ниже его точки плавления, чтобы лазеру было легче поднять температуру выбранных областей до точки плавления. [6]
В отличие от некоторых других процессов аддитивных производства, такие как стереолитографии (SLA) и моделирование методом наплавления (FDM), которые наиболее часто требуют специальных вспомогательных структур для изготовления нависающих конструкций, ЛСН не нужен отдельный питатель для поддержки материала , поскольку часть строится всегда окружен неспеченным порошком, что позволяет создавать ранее невозможные геометрические формы. Кроме того , поскольку камера аппарата всегда заполнена порошковый материал изготовление нескольких деталей имеет гораздо меньшее влияние на общей сложности и стоимости конструкции , потому что с помощью метода , известного как " Вложенные'несколько частей могут быть расположены так, чтобы соответствовать границам машины. Однако один аспект конструкции, который следует учитывать, заключается в том, что с помощью SLS «невозможно» изготовить полый, но полностью закрытый элемент. Это связано с тем, что неспеченный порошок внутри элемента нельзя было слить.
Поскольку срок действия патентов начал истекать, стали доступны доступные домашние принтеры, но процесс нагрева по-прежнему является препятствием, поскольку потребляемая мощность достигает 5 кВт, а температуру необходимо контролировать в пределах 2 ° C для трех этапов предварительного нагрева и плавления. и хранение перед удалением. [1]
Материалы [ править ]
Качество печатных структур зависит от различных факторов, включая свойства порошка, такие как размер и форма частиц, плотность, шероховатость и пористость. [7] Кроме того, распределение частиц и их термические свойства сильно влияют на сыпучесть порошка. [8]
Коммерчески доступные материалы, используемые в SLS, бывают в виде порошка и включают, помимо прочего, полимеры, такие как полиамиды (PA), полистиролы (PS), термопластические эластомеры (TPE) и полиарилэфиркетоны (PAEK). [9] Полиамиды являются наиболее часто используемыми материалами SLS из-за их идеальных характеристик спекания в качестве полукристаллического термопласта , что приводит к деталям с желаемыми механическими свойствами. [10] Поликарбонат (ПК) представляет большой интерес для SLS из-за его высокой ударной вязкости, термической стабильности и огнестойкости; однако такие аморфныеполимеры, обработанные SLS, как правило, приводят к получению деталей с ухудшенными механическими свойствами, точностью размеров и, таким образом, ограничиваются применениями, где они не имеют большого значения. [10] Металлические материалы обычно не используются в SLS с момента развития селективного лазерного плавления .
Производство порошков [ править ]
Частицы порошка обычно производятся путем криогенного измельчения в шаровой мельнице при температурах значительно ниже температуры стеклования материала, которая может быть достигнута путем проведения процесса измельчения с добавлением криогенных материалов, таких как сухой лед (сухое измельчение) или смеси жидкостей. азот и органические растворители (мокрый помол). [11] В результате процесса могут быть получены частицы сферической или неправильной формы диаметром до пяти микрон . [11] Гранулометрический состав порошка обычно гауссовский.и варьируются от 15 до 100 микрон в диаметре, хотя это может быть изменено для соответствия разной толщине слоя в процессе SLS. [12] Покрытия с химическим связующим могут быть нанесены на порошковые поверхности после обработки; [13] эти покрытия помогают в процессе спекания и особенно полезны для формирования деталей из композиционных материалов, таких как частицы оксида алюминия, покрытые термореактивной эпоксидной смолой . [12]
Механизмы спекания [ править ]
Спекание в SLS в основном происходит в жидком состоянии, когда частицы порошка образуют слой микроплавления на поверхности, что приводит к снижению вязкости и образованию вогнутой радиальной перемычки между частицами, известной как сужение, [13] из-за реакция материала на снижение его поверхностной энергии. В случае порошков с покрытием цель лазера - расплавить поверхностное покрытие, которое будет действовать как связующее. Твердотельное спекание также является фактором, хотя и в гораздо меньшей степени, и происходит при температурах ниже температуры плавления материала. Основной движущей силой этого процесса снова является реакция материала на понижение состояния свободной энергии, что приводит к диффузии молекул через частицы.
Приложения [ править ]
Технология SLS широко используется во многих отраслях промышленности по всему миру из-за ее способности легко создавать сложные геометрические формы с минимальными производственными усилиями или без них. Чаще всего он применяется в прототипах деталей на ранних этапах цикла проектирования, таких как модели для литья по выплавляемым моделям, автомобильное оборудование и модели аэродинамических труб . SLS также все чаще используется в ограниченном производстве для производства деталей конечного использования для аэрокосмической, военной, медицинской и электронной техники. В цехе SLS можно использовать для быстрого изготовления оснастки, приспособлений и приспособлений . [14]Поскольку этот процесс требует использования лазера и другого дорогостоящего и громоздкого оборудования, он не подходит для личного или домашнего использования; тем не менее, он нашел применение в искусстве [ссылка художника EOS с изображениями].
Преимущества [ править ]
- Слой из спеченного порошка полностью самонесущий, что позволяет:
- большие углы нависания (от 0 до 45 градусов от горизонтальной плоскости)
- сложные геометрические формы, глубоко встроенные в детали, такие как конформные каналы охлаждения
- серийное производство нескольких деталей, производимых в трехмерных массивах, этот процесс называется раскрой
- Детали обладают высокой прочностью и жесткостью
- Хорошая химическая стойкость
- Различные возможности отделки (например, металлизация, эмаль для печей, вибрационное шлифование, окраска ванн, склеивание, порошковое покрытие, флокирование)
- Биосовместимость согласно EN ISO 10993-1 [15] и USP / уровень VI / 121 ° C
- Сложные детали с внутренними компонентами могут быть построены без захвата материала внутри и изменения поверхности после удаления опоры.
- Самый быстрый процесс аддитивного производства для печати функциональных, долговечных, прототипов или деталей конечного пользователя
- Широкий выбор материалов с характеристиками прочности, долговечности и функциональности.
- Благодаря надежным механическим свойствам детали часто могут заменять типичные пластмассы для литья под давлением.
Недостатки [ править ]
- детали имеют пористую поверхность; они могут быть запечатаны несколькими различными методами последующей обработки, такими как цианоакрилатные покрытия [16] или горячим изостатическим прессованием .
См. Также [ править ]
- 3D печать
- Настольное производство
- Цифровой производитель
- Прямое цифровое производство
- Fab lab
- Моделирование наплавленного осаждения (FDM)
- Мгновенное производство , также известное как прямое производство или производство по запросу
- Быстрое производство
- Быстрое прототипирование
- RepRap Project
- Изготовление твердых материалов произвольной формы
- Стереолитография (SLA)
- Универсальный конструктор фон Неймана
Ссылки [ править ]
- ^ Декард, К., «Способ и устройство для производства деталей путем избирательного спекания», патент США 4863538 , поданный 17 октября 1986 г., опубликованный 5 сентября 1989 г.
- ^ Лу, Алекс и Гросвенор, Кэрол " Селективное лазерное спекание, рождение отрасли ", Техасский университет , 7 декабря 2012 г. Проверено 22 марта 2013 г.
- ^ US5597589
- ^ Housholder, Р., "Molding Process", патент США 4247508 , поданный 3 декабря 1979, опубликованный 27 января 1981 года.
- ^ «Руководство по проектированию: селективное лазерное спекание (SLS)» (PDF) . Xometry .
- ^ Прасад К.Д.В. Ярлагадда; С. Нараянан (февраль 2005 г.). GCMM 2004: 1-я Международная конференция по производству и менеджменту . Alpha Science Int'l. С. 73–. ISBN 978-81-7319-677-5. Проверено 18 июня 2011 года .
- ^ Leturia, M .; Benali, M .; Lagarde, S .; Ronga, I .; Салех, К. (01.02.2014). «Характеристика текучести когезионных порошков: сравнительное исследование традиционных и новых методов испытаний» . Порошковая технология . 253 : 406–423. DOI : 10.1016 / j.powtec.2013.11.045 . ISSN 0032-5910 .
- ^ Leu, Ming C .; Паттнаик, Шашваташиш; Хилмас, Грегори Э. (март 2012 г.). «Исследование процесса лазерного спекания для изготовления деталей из диборида циркония произвольной формы» . Виртуальное и физическое прототипирование . 7 (1): 25–36. DOI : 10.1080 / 17452759.2012.666119 . ISSN 1745-2759 . S2CID 137566316 .
- ^ «Высококачественные пластмассовые материалы для аддитивного производства» . www.eos.info . Проверено 19 февраля 2019 .
- ^ а б Клоос, Стефани; Dechet, Maximilian A .; Пойкерт, Вольфганг; Шмидт, Йохен (июль 2018 г.). «Производство сферических полукристаллических микрочастиц поликарбоната для аддитивного производства путем разделения фаз жидкость-жидкость». Порошковая технология . 335 : 275–284. DOI : 10.1016 / j.powtec.2018.05.005 . ISSN 0032-5910 .
- ^ a b Шмидт, Йохен; Плата, Мигель; Трегер, Сулай; Пойкерт, Вольфганг (сентябрь 2012 г.). «Производство полимерных частиц размером менее 5 мкм мокрым измельчением». Порошковая технология . 228 : 84–90. DOI : 10.1016 / j.powtec.2012.04.064 . ISSN 0032-5910 .
- ^ а б Ян, Цюпин; Ли, Хуэйчжи; Чжай, Юбо; Ли, Сяофэн; Чжан, Пэйчжи (13.08.2018). «Синтез покрытых эпоксидной смолой композитов Al2O3 для селективного лазерного спекания 3D-печати». Журнал быстрого прототипирования . 24 (6): 1059–1066. DOI : 10,1108 / гн-09-2017-0189 . ISSN 1355-2546 .
- ^ a b Kruth, J-P .; Mercelis, P .; Van Vaerenbergh, J .; Froyen, L .; Ромбоутс, М. (февраль 2005 г.). «Механизмы связывания в селективном лазерном спекании и селективном лазерном плавлении». Журнал быстрого прототипирования . 11 (1): 26–36. DOI : 10.1108 / 13552540510573365 . ISSN 1355-2546 .
- ^ «Обзор приложений для селективного лазерного спекания | Краткие руководства» . www.3dsystems.com . Проверено 25 февраля 2019 .
- ^ Биологическая оценка медицинских изделий - Часть 1: Оценка и тестирование в процессе управления рисками (ISO 10993-1: 2009) . Международная организация по стандартизации (ISO). 2009. OCLC 839985896 .
- ^ https://www.anubis3d.com/technology/selective-laser-sintering/
Внешние ссылки [ править ]
- DMLS - ИСТОРИЯ РАЗВИТИЯ И СОСТОЯНИЕ ТЕХНИКИ
- Селективное лазерное спекание, зарождение отрасли
- Лазерное спекание, плавление и другие - SLS, SLM, DMLS, DMP, EBM, SHS